Functions of Material Management
Functions
of Material Management
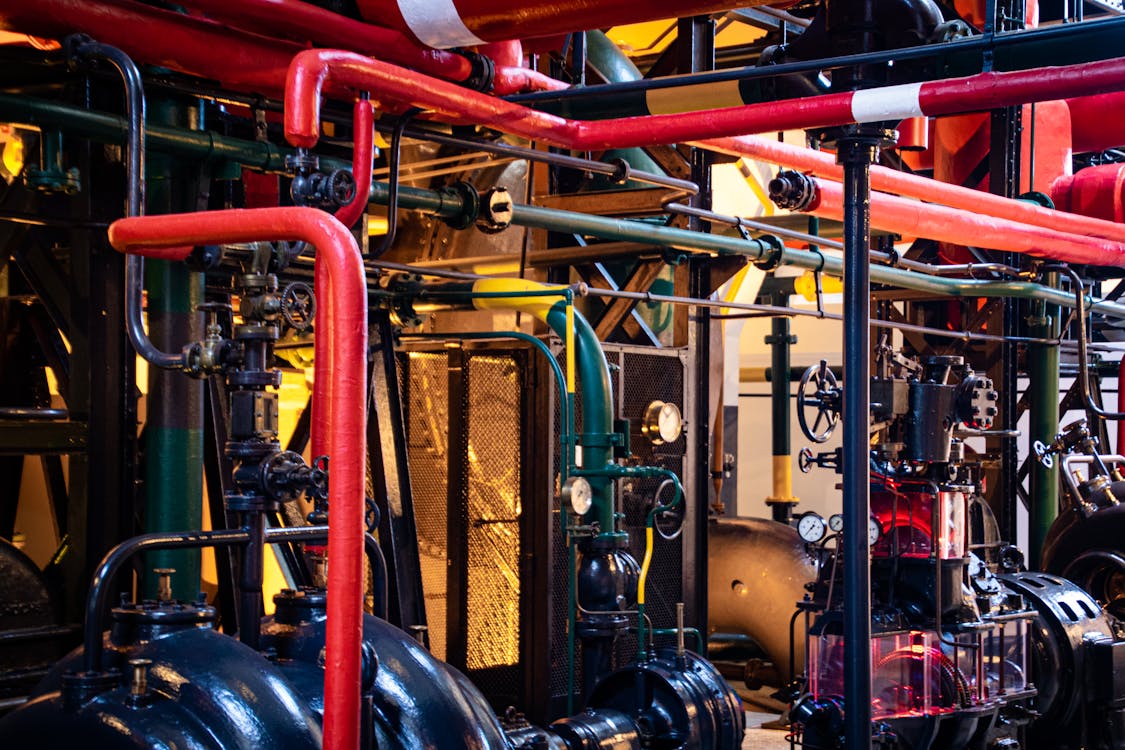
(I)
Primary Functions
To
meet the primary objectives, the primary functions of the materials management
are given as follows:
(i)
Materials Requirements
Planning (MRP) Planning of materials
requirements in manufacturing is a necessary function in any organization, as
inventory of materials involve about 60% of the total investment of the
organization. The profit earned depends on the utilization of these materials
and reducing the inventory of the materials. The latest technique used is
called Just in Time (JIT) is referred practically to no inventory. However, in
the present situations in any of the organization particularly manufacturing
organization, it is not absolutely possible to keep no inventory of materials
required for production.
The MRP is a technique used to plan the materials
starting from the raw materials, finished parts, components, sub-assemblies and
assemblies as per Bill of Materials (BOM) to procure or produce them to support
a Master Production Schedule (MPS). It is used on computers productively by any
company that uses a MPS to manufacture products that require assemblies,
components and materials to produce the final products. The MPS is exploded using
the bills of materials to determine requirements of lower-level assemblies,
components, finished parts and raw materials. It plans orders to meet these
needs.
(ii)
Purchasing
All the organizations
needs an efficient and economic purchasing and procurement of its various
supplies of materials from the suppliers. The materials management department
has to perform this function of purchasing and procurement of materials very
efficiently. Since 50% to 60% of sales turnover is spent on the purchase of
various materials, the amount of profit earned on this sales very much depends
how economically the materials are purchased and utilized in the organization.
The profitability depends on the efficiency by which this particular function
of purchasing and procuring the requisite materials at appropriate time will be
done and its availability is assured.
The function of
purchasing can be stated as follows:
(1) The requisition of material is
necessary by proper authority to initiate its purchase.
(2) To select proper
supplier for the materials requisitioned, before placing an order.
(3) To
negotiate about the price of the material from the supplier and it will be
purchased at the cheapest price.
(4) The quality of material must be assured
and should not be compromised with the cost of the material.
(5) The material
should be purchased of right quantity and right quality at proper time at the
cheapest cost.
(6) To set the proper purchase policy and procedure.
(iii)
Inventory Planning and Control
The modern concept of inventory
planning is that the materials should be purchased and brought in the stores
just before it enters the production or sold out so that inventory cost is
negligible. The zero inventories are the ideal planning. There are three types
of inventories.
(i) Raw materials
(ii) Purchased parts and components
(iii)
Finished Goods
The inventory control of
these various materials lies with the materials management department,
production department and sales department. Inventory at different levels is
necessary to make sure about the availability of all these types of materials
and goods and their proper flow from one facility to another at different
levels of production centers in a manufacturing concern. The storing of various
types of materials and parts as inventory is therefore very essential before
its delivery and use at different production centers. This involves inventory
planning and control of materials in the stores department. Many a time, the
supplier may not be in a position to supply the materials of the ordered
quantity at the proper time. To maintain the continuity in production and line
balance in assembly work, the various types of inventories are necessary to be
maintained and kept in the stores. The raw materials before being supplied to a
production process, some of it is sent to store as inventory and rest is sent
to production facility as per its requirements and in the same way, various
parts manufactured and assembled as components and assemblies are also stored
as finished parts inventories at the different places in the stores. The final
products before being supplied to the customers are also stocked as inventory
of the final products of the organization to meet the fluctuating demand and to
regularize the supplies in the market. Thus, the inventory control is a very
important function of the materials management department. The various types of
inventory models are developed for the different materials to economise the
purchase, supply, inventory control and production control to analyze and
optimize the costs involved in ordering, set-up and inventory carrying of
materials required in the production.
(iv)
Ascertaining and Maintaining the Flow
and Supply of Materials
Distribution of materials
requisitioned by the various production centers and other departments must be
ascertained and its flow and continuity of supply must be maintained by the
materials management department. Insufficient or zero inventories many times
create the situations of stock-outs and leads to stoppage of production.
Failure of materials handling devices is also responsible for disruption of
material supplies. Alternatives or emergency supply systems can be used for
assuring production lines to continue. Uncertainty in demand and production
quantity is the main factor. As the customer requirements as per his needs and
liking, are changing very fast. The management has to maintain continuity in
production to meet this uncertainty in demand and control the situation by
proper flow of materials supply and distribution at various production
facilities and other departments as per changes in production quantity.
(v)
Quality Control of Materials
The quality of the
product manufactured by the organization depends upon the quality of the
materials used to manufacture that product. It is a very important and
necessary function of materials management to purchase the right quality of
materials. The inspection, quality control, simplification, specification, and
standardization are the activities which are to be followed for the measurement
of quality of the materials. The quality assurance is decided by inspection and
checking. The various properties of materials as per their specifications and
standard. The size and dimensional measurements within tolerance limits assures
the interchangeability and reliability of components and parts. Quality is
largely determined by consumer taste and liking. The market is under buyer’s
control. Customer decides the quality of the product. Material quality control
aims at delivering product at higher and higher quality at lower cost. The
product will be specified not only by its dimensional accuracy but its quality
standards, durability and dependability, high performance, reliability and
aesthetic value. Each of this factor aids cost to the product. In order to
achieve high quality, the materials input to the product should be of high
quality, which will have higher cost. The performance decides the reliability,
which is obtained through high quality production. The performance is checked
by quality inspection and accuracy. This also aids cost to the product. The
quality of the materials also decides the selection of vendors and the
relationship between buyers and suppliers. The specifications, size and quality
of materials must be referred and if possible the standard should be followed
for specifications and sizes. The types of tests required for assuring the
quality should be specified and conducted to establish the standards.
(vi)
Departmental Efficiency
The objective of this function is to
ensure the efficiency of the system adopted. If the system and procedure
adopted for materials management are inefficient or faulty, none of the
objectives mentioned above can be fulfilled, howsoever the procedure may be
good. In order to maintain the things in proper way as per planning an
efficient control is necessary in the department over each and every process.
Management Information System (MIS) and feedback control at every stage of
working must be adopted to control and make the management and employee work as
efficiently as possible to achieve the best results.
(II)
Secondary Functions
There can be number of secondary
functions. Some of them are discussed below:
(i)
Standardization
and Simplification
The standards and specifications of various types of materials are fixed by
design and technical department of the organization and they are followed by
production department. Standards define the quality, reduction in sizes and
variety, interchangeability of parts and products. It ensures efficient utilization
of materials and reduces wastage. Standard materials are always available at
reasonable cost. It also helps purchasing department in selection of materials
and vendors. If less variety of items purchased and put in the stores the types
of inventories will be reduced and in this way the cost of carrying the
inventories in the stores will be reduced. The objective of this function will
be to produce standard product reducing the overall cost of the product.
(ii)
Design
and Development of the Product
The variety in product and functionality are the important factors to promote
the sales of a product. The new techniques of designing a product using
Computer Aided Design (CAD) has made possible to develop variety of products at
faster rate. The new technological development in manufacturing using Computer
Aided Manufacturing (CAM) can produce variety of products at much faster rate
with all types of flexibility in the manufacturing as compared to conventional
methods. Materials management department has to act according to use of such
variety of materials to produce variety of parts and ensure the supply of such
materials. It should also be decided how to purchase and produce such variety
of products with flexibility and economic cost.
(iii) Make
and/or Buy Decisions
These types of decisions are the policy decisions of the management. The
capacity of the organization and the various facility developed by the
organization to manufacture various items is the main objective of every
organization. This is the important planning activity of every undertaking. But
when a company grows fast, its sales increases at rapid rate then it becomes an
important matter to decide whether the company should buy the parts and
components or increase and establish its facilities to cope up with the
increased demand and sales. This will be greatly concern to materials
management department. It will help in selecting the suppliers to buy the items
at reduced cost. The material evaluation, its availability, alternative
materials selection, procurement and inventory control are the functions
influence the make and buy decisions. The make and buy decisions are largely
based on cost economics and cost benefit analysis made by the organization
using the existing production capacity of labor, skill and machines available
with the factory and how best they can be utilized.
(iv)
Coding
and Classification of Materials
This is an important function of the materials management to help the
production and purchasing department of every organization. It uses its own
methods of classification of materials used to manufacture the product or a
company selling various goods. ABC analysis is one of the simple and standard
method used by most of the firms for classification and storing their variety
of materials. The materials are recognized to purchase and store as an
inventory by its codes and nomenclatures. The various methods of coding are
used by every organization to control the variety of materials and its quantity
and price rates.
(v)
Forecasting
and Planning
Materials
requirements planning is based on correct forecasting of sales and demand of
the products in the market. The market fluctuations are to be observed to
control production of the organization. The various methods of forecasting are
available and the materials management department can choose the one which
gives the best results to the company. Forecast of future demand of sales sets
the planning of materials supply. Analytical methods are adopted for systematic
forecasting and planning to procure the various materials required for
production. In case of fluctuating demands, there can be uncertainties in
supply as well. This can be overcome by maintaining the proper quantity in
inventory of short supply materials at proper time. The different techniques
available to use correct forecasting have to be utilized by materials manager
to plan the procurement, purchase, supply, managing the outside and inside
transport and storing of the materials to maintain the supply chain lines at
every production facility to meet the changes in production quantity and
schedule of production to meet the fluctuating demand of sales of products
manufactured by the organization.
Reference
:
Comments
Post a Comment